Spun Products
Spinco Metal Products, Inc. is an industry leader in spun copper driers and drier assemblies. Air conditioning and refrigeration OEM’s see us as a quality manufacturer, and our customers continue to experience the superior performance our products offer. We are proud to have developed the Dura Sieve Drier, which is a solid core product in a copper shell where maximum filtration of particulate contamination and maximum absorption of moisture results. Allow us to find you the copper spun desiccant drier that is right for your application.
Important factors in determining suitability of refrigerant driers are:
- Horsepower of the compressor
- Total amount of your system refrigerant charge
- Maximum operating temperature of your system
- Maximum operating pressure of your system
- Total system moisture
- Type of refrigerant used in your system
Selection of a Drier
The suitability of a refrigerant drier for use with any particular system or equipment depends upon a number of factors. It is the responsibility of the OEM to determine suitability. We make no representation or warranty, express or implied, that any particular drier is suitable for any particular purpose. The guidelines presented on this page are supplied only for the purpose of assisting the OEM’s in determining the types of driers for use with their applications.
These guidelines cannot take into account all of the possible combinations of factors which could affect the suitability of a drier for use in connection with particular equipment. OEM’s should test driers with their specific equipment. Testing of driers to be included in the systems employing the new POE oils is especially advisable, due to the effect of such oils on refrigerants.
Compressor horsepower and typical charge
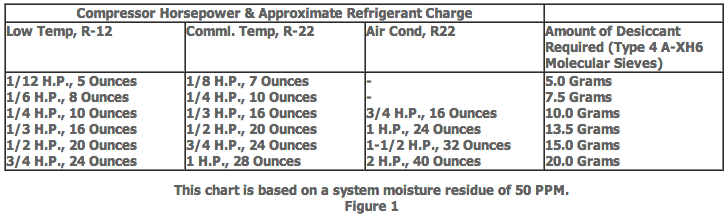
Maximum Operating Temperature

Maximum Operating Pressure
To effectively choose a drier that has a wall thickness adequate to withstand the maximum internal pressure, the maximum operating pressure of your system must be known. Wall thickness must be at least five times the maximum operating pressure
Total System Moisture
Our customers should identify the amount of total system moisture present in their particular system. System moisture can vary based on many factors. It is more important that our customers follow procedures consistent with assuring that the identified system moisture isn’t exceeded. This is especially important with respect to equipment using the new refrigerants.
Refrigerant Type
It is very important to identify the correct desiccant based on the refrigerant being used. The chart below is a guide to the compatible desiccant for your use.
For the amount of desiccant that should be used in driers, you should contact the compressor manufacturers. Specifications can vary from one company to another. Spinco will make whatever is specified by the compressor manufacturer.
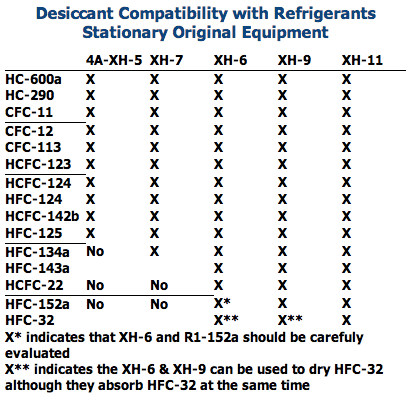
Selecting An Accumulator / Receiver:
A refrigerant accumulator is generally selected based on the volume of refrigerant to be held and the maximum operating pressure of the system.
Volume of Refrigerant
This is necessary in calculating the diameter and length of the accumulator shell. The accumulator size will vary with the precision with which the system charge is measured, the quantity of refrigerant charged into the system and the temperatures involved. The deciding factor is the suction line temperature, as far as comparing refrigerant volume is concerned.
Operating Pressure
Normally the accumulator is chosen which has a minimum burst pressure that is at least five times the maximum operating pressure. Therefore, the maximum operating pressure must be known.
We will be glad to work with your engineers to develop the accumulator design your equipment requires. Custom requests are not uncommon. Accumulator assemblies incorporating tubes and screen assemblies are commonly manufactured by Spinco. Our compressor accumulators are made to the rigid specifications of the compressor manufacturers. We welcome all inquiries.
Mufflers
Spinco’s discharge mufflers are designed to smooth out the pulsations generated by the reciprocating compressor. By reducing the magnitude of these pulsations, the noise level throughout the system is reduced, as is vibration.
The Spinco Series 200 mufflers are heavy duty components having shell spun from .060″ wall copper tubing. Minimum burst pressure is 2300 p.s.i. Baffle plates are tightly pressed inside the shell, with their holes oriented to permit drainage through the outlet tube when the muffler is installed horizontally. The muffler also may be mounted vertically, with the outlet tube down.
When installing the muffler, the inlet should be connected to the discharge side of the compressor, and the outlet connected to the condenser.
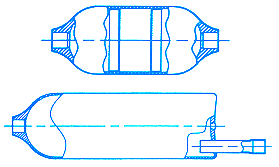
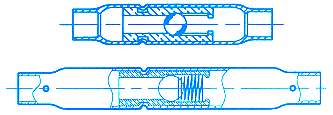
Check Valves
The mechanical strength and simplicity of this design assures permanent, trouble free functioning of the check valves required in heat pumps. The valve opens without resistance when the flow through the valve is horizontal or downward. The ball rolls free in the brass track as it would, unrestricted, in the similar race of a ball bearing. When flow is upward, only the lightweight of the stainless steel ball resists the fluid flow. This is less resistance than is imposed by the usual valve closing spring. Thus, this valve may be installed in any position.
Fluid flowing with a small angle of deflection around a hardened and polished stainless steel ball provides high flow capacity in check valves of much smaller diameter. The flow resistance is much less than around a right angle bend, and is substantially less than valves having a flow switch back through a narrow opening around the circular edge of a flat disc.
Spinco check valves are designed for working pressures up to 600 p.s.i. in heat pump systems up to ten tons.
Copper check valves are most commonly used when cost is a factor and a leak rate of up to 750 cc’s per minute at 100 p.s.i. is tolerable. Our Brass Division offers other styles with more precise flow check capabilities.
Strainers – Strainer / Distributors – Distributors
A refrigerant strainer should be chosen on the basis of these two system characteristics:
Type and amount of contaminants that can be expected to develop in the system.
Maximum operating pressure of the system.
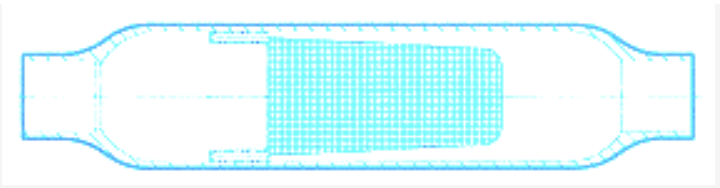
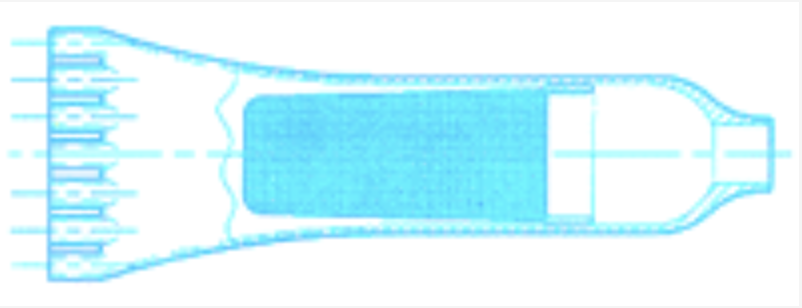
Contaminants:
It is necessary to know the size and quantity of the contaminants to make a proper strainer selection. This is so you may choose a strainer having an amount of screen area sufficient to trap and hold foreign particles that accumulate during the life of the unit, and yet permit the refrigerant flow to continue without excessive pressure drop.
This is a function of the residue on the inside of the component parts, the amount of care exercised during assembly, and the size or capacity of the system.
Strainer wire cloth materials are stainless steel, brass or phosphor bronze. The woven material sizes range from 100 x 90 to 150 x 140 mesh. Brass or stainless steel dutch weave is used in special applications where small micron filtration is required.
Screen area will depend, to a large extent, on the size or the capacity of the system. Strainers to be placed in the suction line should have enough area to result in nearly zero pressure drop.
All Spinco refrigerant strainers have the screen securely crimped into a collar or screen-holder before it is pressed into the strainer shell.
Maximum Operating Pressure:
As in the case of driers, it is necessary to know the maximum operating pressure to select a strainer of sufficient wall thickness. Again, the minimum burst pressure should be five times the maximum operating pressure.
Manufacturing Standards:
To assure the highest quality products, Spinco has developed stringent quality requirements for material. The following information provides further detail regarding our manufacturing practices.
Screen Materials:
Only pre-cleaned premium wire cloth materials are used. Assemblies are certified to a minimum 28 lb. pressure test. Our specifications assure maximum protection from contamination, corrosion, and screen failure.
Spun Ends:
For the benefit of proper soldering we assure a minimum “lay-in-land” equal to the width of the hole whenever dimensionally possible. We offer spun off dimple tube stops or the assurance of specific tube insertion depths.
Multiple Outlet and Inlet Formed Ends:
When dimensionally possible we assure a minimum “lay-in-land” of 5/16″ and that the formed sides meet.
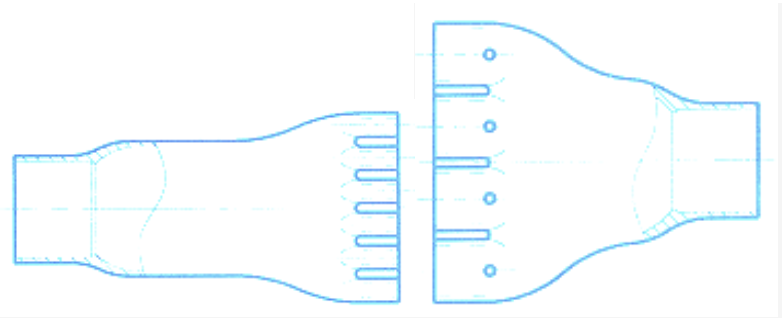
For a free estimate or for more information about spun copper driers and drier assemblies, contact us at 315-331-6285 or take a look at our products.
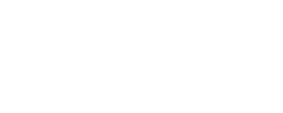
Spinco Metal Products, Inc. Headquarters
Sitemap
Contact
Phone: 315-331-6285
Fax: 315-331-9535
Email: crios@spincometal.com
Business Hours
Monday - Friday
8 AM - 5 PM